Water jet cutting is an innovative and efficient technique used in the fabrication of shower glass. This method utilizes a high-pressure stream of water, often combined with abrasive materials, to cut through various materials, including glass.
At Qingdao Migo Glass Co., Ltd, a company specializing in the custom processing and production of shower glass, this technology is employed not only for cutting the glass panels but also for creating precise holes for handles and hinge cut-outs. Migo Glass provides a one-stop solution for bathroom glass, aiming to collaborate with online retailers, installers, glass shops, and glass contractors.
How Water Jet Cutting Works
- High-Pressure Water Stream
Water jet cutting systems generate a stream of water at extremely high pressures, typically between 30,000 to 90,000 psi. This intense pressure allows the water to cut through materials with precision.
- Abrasive Addition
For cutting glass, abrasives such as garnet are often added to the water stream. This combination enhances the cutting capability, enabling the jet to slice through thick materials more effectively.
- Computer Numerical Control (CNC)
Most modern water jet systems are CNC-operated, allowing for precise and intricate designs to be cut. This technology ensures that shower glass can be fabricated to exact specifications, accommodating various shapes and sizes.

Benefits of Water Jet Cutting for Shower Glass
Precision and Accuracy:
Water jet cutting offers exceptional precision, allowing for intricate designs and custom shapes. This is particularly important for shower glass, where accurate dimensions are crucial for proper fitting.
Smooth Edges:
The cutting process results in smooth edges, eliminating the need for extensive finishing work. This is beneficial for both aesthetic appeal and safety, as sharp edges can pose a risk to users.
Minimal Heat Affected Zone:
Unlike traditional cutting methods, water jet cutting generates minimal heat. This is vital for glass fabrication, as excessive heat can cause thermal stress, leading to cracks or breakage.
Versatility:
Water jet cutting can be used on various types of glass, including tempered, laminated, and even ceramic materials. This versatility makes it an ideal choice for different shower glass applications.
Eco-Friendly:
The water jet cutting process produces minimal waste and does not involve harmful chemicals, making it an environmentally friendly option for glass fabrication.
Water Jet Cutting in Shower Glass Fabrication
Custom Shower Enclosures:
Water jet cutting allows manufacturers to create custom shower enclosures that fit unique bathroom layouts. This customization enhances the overall aesthetic and functionality of the space.
Decorative Elements:
The precision of water jet cutting enables the incorporation of decorative elements, such as patterns or logos, into shower glass. This adds a personalized touch to bathroom designs.
Panel Cutting:
Large sheets of glass can be cut into smaller panels for various applications, including sliding shower doors and fixed partitions. This efficiency reduces material waste and optimizes production.
Complex Shapes:
The technology allows for the creation of complex shapes, such as curved or angled glass, which can enhance the design of modern bathrooms.
Fabrication of Holes and Cut-Outs:
At Migo Glass, the holes for handles and hinge cut-outs are all fabricated using water jet cutting. This ensures that the openings are perfectly sized and positioned, allowing for easy installation and a clean finish. The precision of water jet cutting means that these critical components can be integrated without compromising the integrity or aesthetics of the glass.
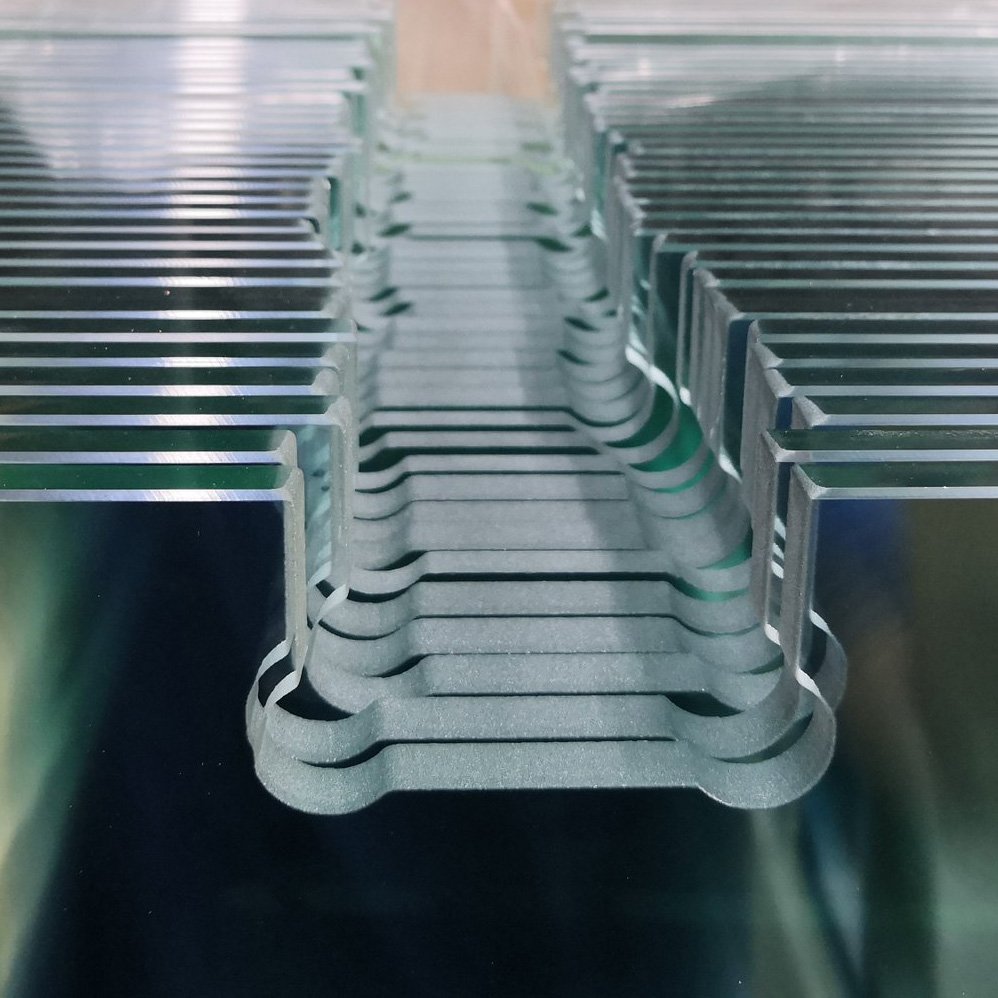
About Qingdao Migo Glass Co., Ltd
Qingdao Migo Glass Co., Ltd is an integrated glass factory focused on the custom processing and production of shower glass for export. With a commitment to providing comprehensive bathroom glass solutions, Migo Glass aims to collaborate with online retailers, installers, offline glass shops, and glass contractors. By leveraging advanced technologies like water jet cutting, Migo Glass ensures that its products meet high standards of quality and design, catering to the diverse needs of the modern bathroom market.
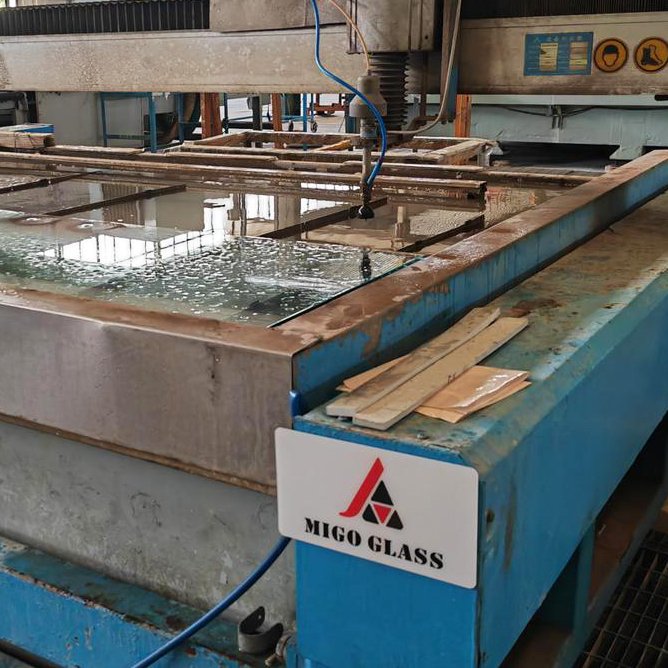
Conclusion
Water jet cutting technology has revolutionized the fabrication of shower glass, offering numerous advantages in precision, efficiency, and environmental impact. The ability to create not only glass panels but also precise holes for handles and hinge cut-outs makes water jet cutting an essential process at Migo Glass. As the demand for custom and stylish bathroom solutions continues to grow, water jet cutting remains a preferred method for manufacturers, enabling them to meet the diverse needs of consumers while maintaining high standards of quality and safety. This technology not only enhances functionality but also contributes to the overall design and user experience of modern shower spaces. Through its commitment to innovation and quality, Migo Glass is well-positioned to lead in the shower glass market.