Shower Glass Laminating
Shower glass laminating is the glass fabrication process used to enhance the safety and durability of glass panels used in bathroom. Glass laminating process sandwiches polyvinyl butyral (PVB), ionic interlayer film (SGP) and other materials between two or more pieces of glass, and processed by high temperature and high pressure. MIGO Glass manufactures and wholesales laminated shower glass at competitive factory price.
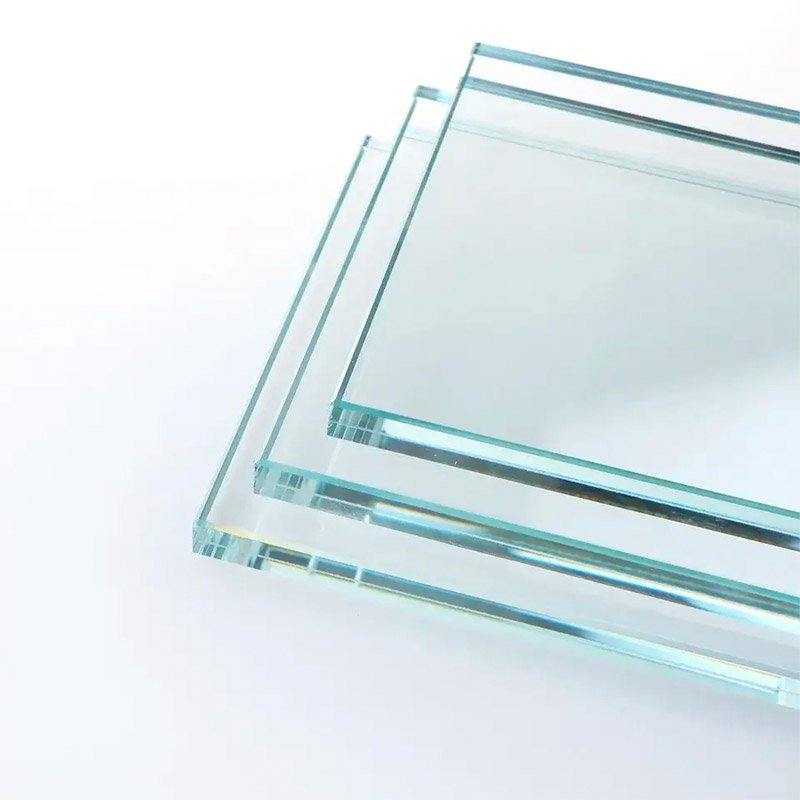
Table of Contents
1. What is Laminated Glass
Laminated glass is also called laminated safety glass. Laminated safety glass (LSG) has at least two panes held together by a polyvinyl butyral (PVB) film. It is also has high impact resistance and puncture resistance.
1.1 Enhenced Safety
Foreign objects usually cannot penetrate it by sudden impact. The glass fragments will not detach from the bonding layer. Laminated shower glass maintains a certain degree of visibility, thus providing a protective safety function.
1.2 Laminated Glass Application
Laminated glass is suitable for shower enclosures to provide a safe and secure barrier. The interlayer can hold the glass fragments together, reducing the risk of injury from sharp shards when breakage.
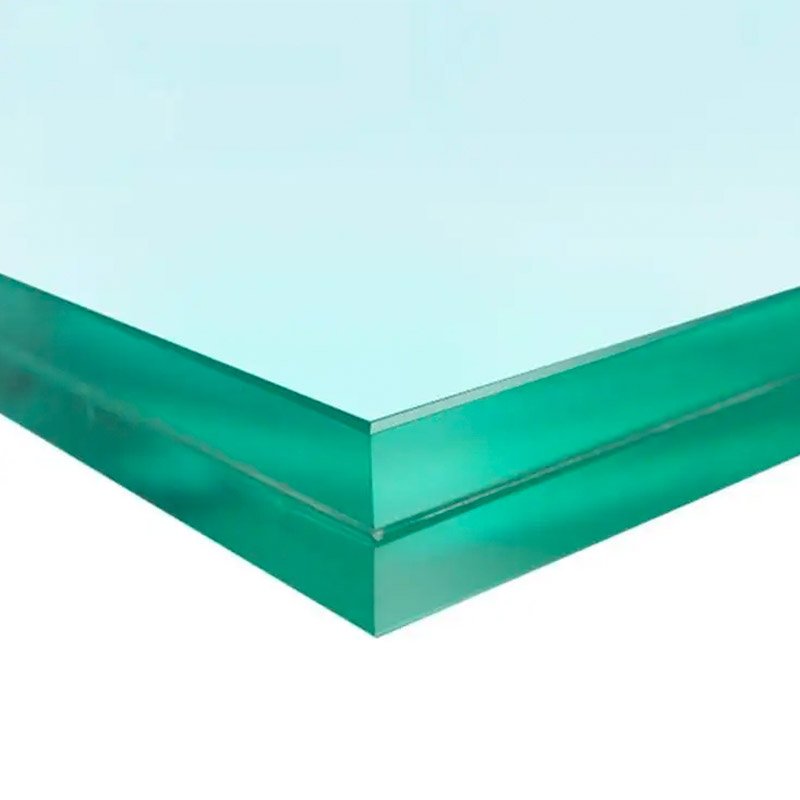
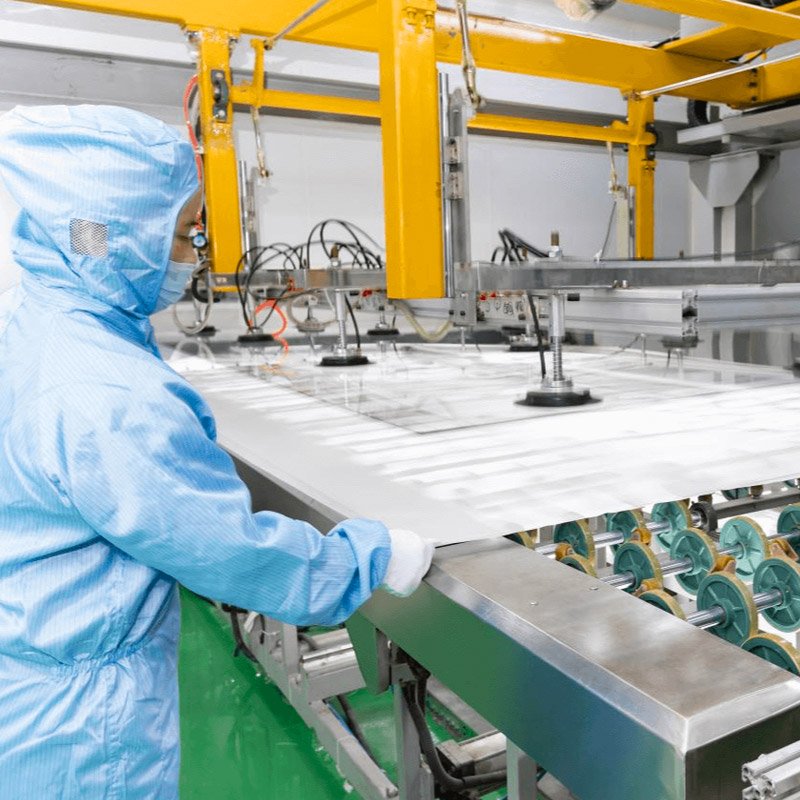
2. How To Laminate Glass
2.1 Glass Laminating Equipment
Glass laminating machine and high pressure autoclave are two important equipment to manufacture laminated shower glass.
The high pressure autoclave for laminated glass is the key equipment in the last process of the laminated glass production line. After the initial pressing, the flat laminated glass or curved laminated glass enters the kettle. They are heated and pressurized to make the glass and film firmly bonded. After cooling, they are tightly bonded to form the finished laminated glass.
Shower glass laminating machine is the special laminated glass manufcturing eqipment to ensure efficient production and consistent quality. It generally consists of loading and unloading, alignment and assembly, heating, pressure, vacuum, and ontrol system, etc.
MIGO Glass has the latest shower glass laminating machines to handle various sizes and thicknesses of glass panels for shower enclosures. These machines streamline the production process, improve efficiency, and ensure the consistent quality and safety of the laminated glass products.
2.2 Shower Glass Laminating Process
MIGO has experinced workers and the special equipment to ensure the highest quality products.
1. Preparation. The glass cut to size and shape. The glass edges should remove any sharpness or roughness.
2. Interlayer Placement. The interlayer material is cut to match the glass panel size. The interlayer between the glass layers covers the entire surface of the glass without any gaps or overlaps.
3. Assembly. The glass panels and interlayer are assembled into a sandwich structure. The layers are carefully aligned to ensure a proper fit.
4. Vacuum Bagging or Autoclave. To remove air bubbles and ensure a strong bond, the assembled glass and interlayer sandwich are placed in high pressure autoclave. heat and pressure are applied to consolidate the layers and create a strong bond in autoclave.
5. Heating and Bonding. The assembled glass and interlayer undergo a heating process to activate the interlayer’s adhesive properties. The heat causes the interlayer to melt and bond with the glass, creating a strong, durable, and transparent composite.
6. Cooling and Finishing. The laminated glass is gradually cooled to stabilize the structure.
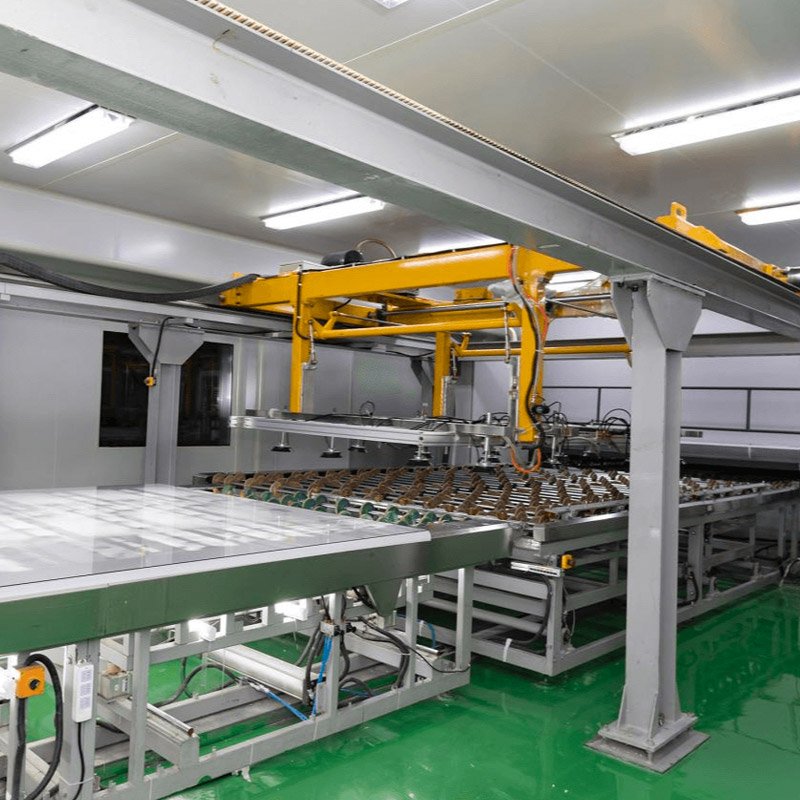